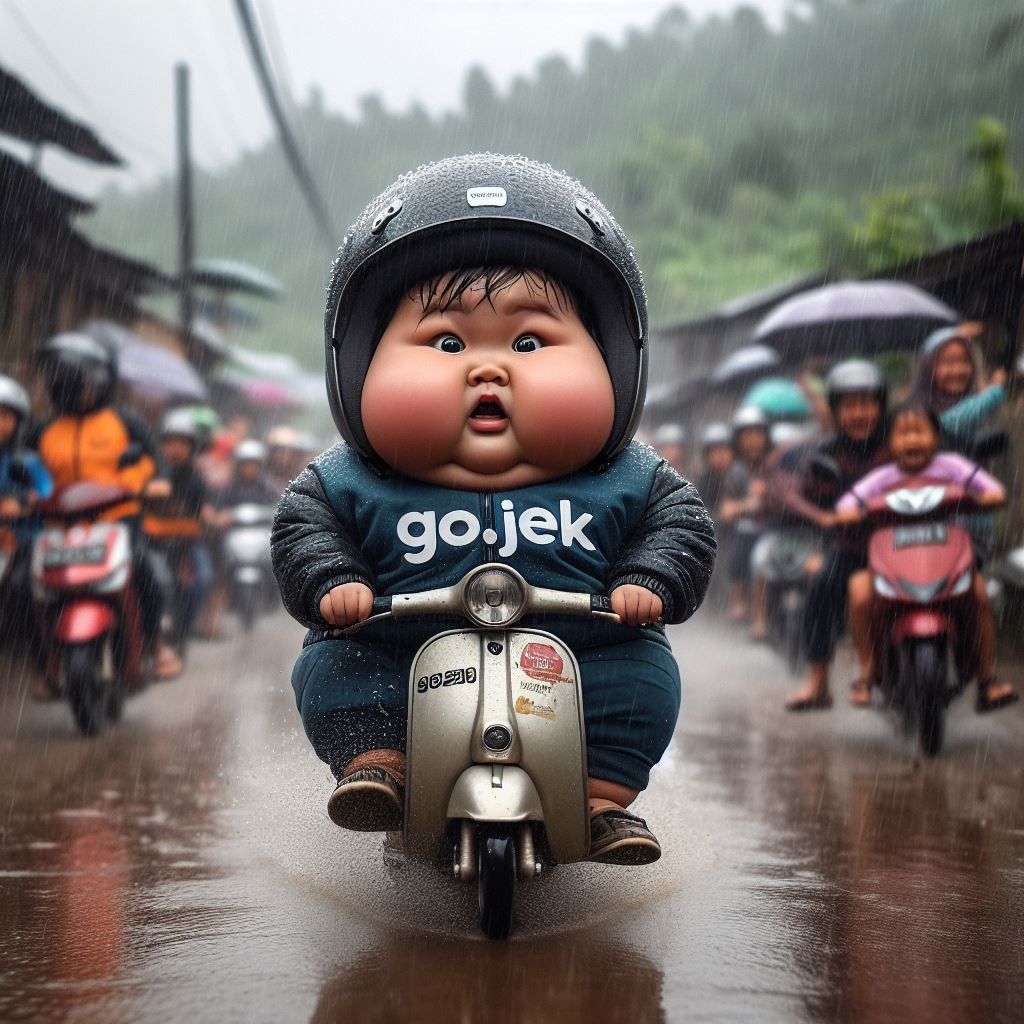
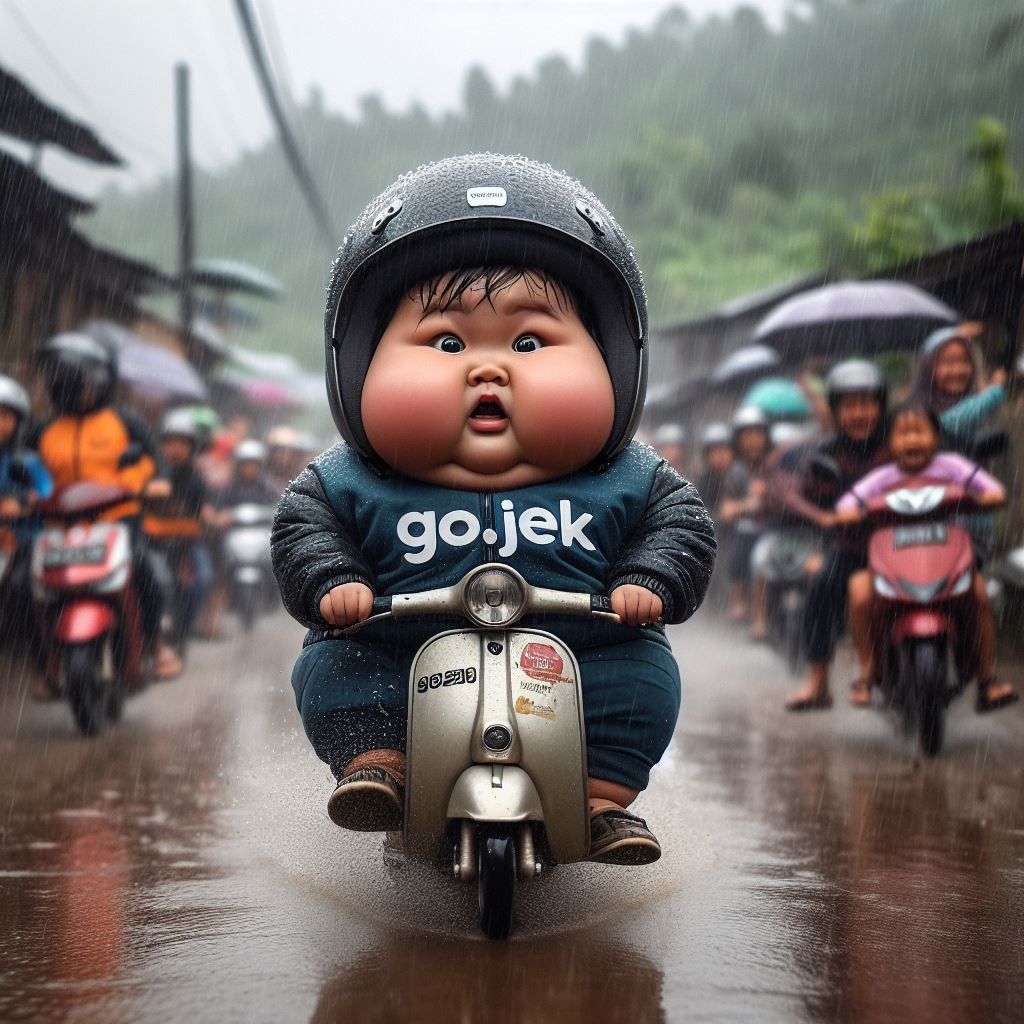

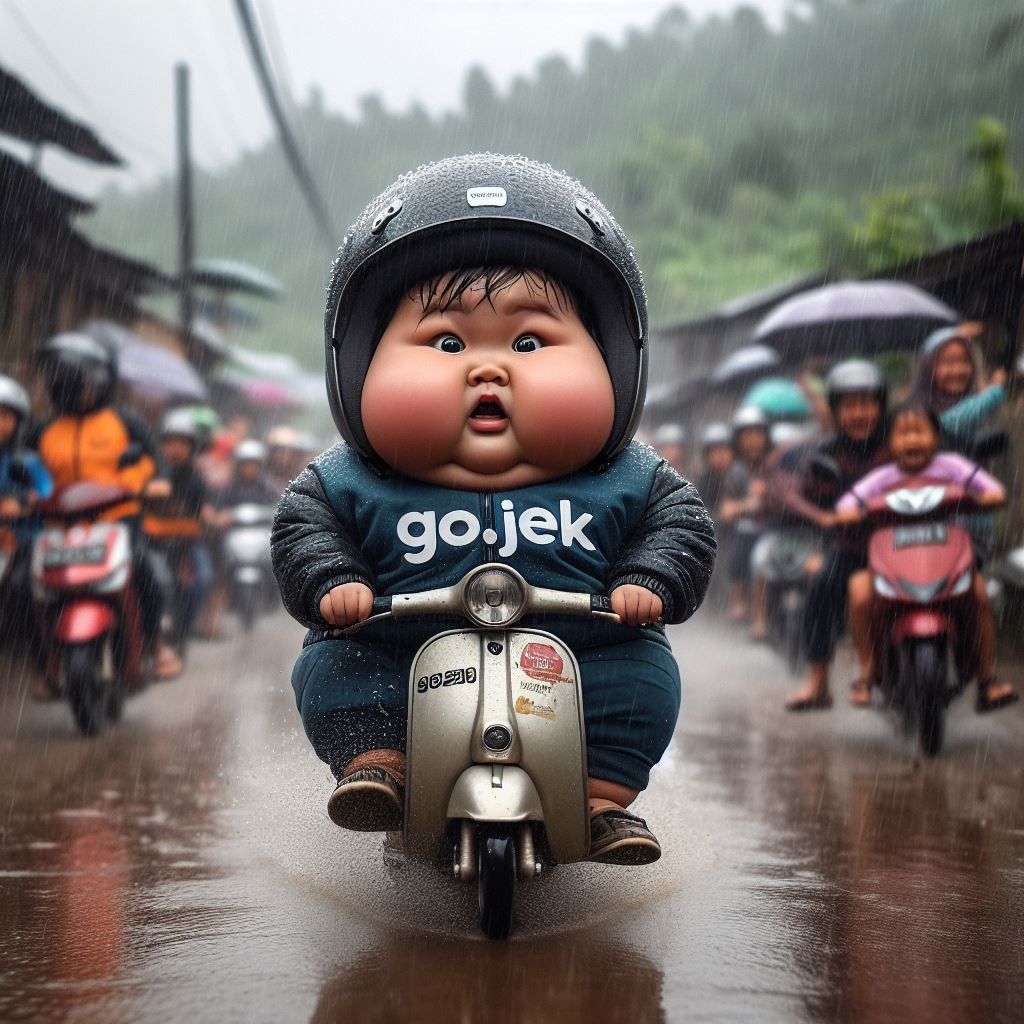
Inatogel X Cartoros Menciptakan Sistem Login Slot Gacor Pertama Di Dunia
Rp 5.000
Warna:
HITAM
Tipe ukuran:
EU
Ukuran:
Pilih ukuran
- 168
- 138
- 88
- 99
- 777
Pilih ukuran
-
INATOGEL
INATOTO
-
INATOGEL DAFTAR
INATOGEL LINK
-
INATOGEL ALTERNATIF
INATOGEL LOGIN
Fitur utama
Artikle
Inatogel X Cartoros Menciptakan Sistem Login Slot Gacor Pertama Di Dunia
Nomer Barang :
99
Merk:
Situs Terpercaya
Tinggi hak :
Platform height :
null
Situs INAtogel :
Tinggi:
Panjang:
Kedalaman:
Strap length :
null
Additional handle :
null
Bahan
technical description